Power Plant System Design Ebook Free
Overview Any power system is prone to 'faults' (also called short-circuits), which occur mostly as a result of insulation failure and sometimes due to external causes. When a fault occurs, the normal functioning of the system gets disturbed. The high current resulting from a fault can stress the electrical conductors and connected equipment thermally and electro-dynamically. Arcs at the fault point can cause dangerous or even fatal burn injuries to operating and maintenance workers in the vicinity. Faults involving one phase and ground give rise to high 'touch' and 'step' voltages posing danger of electrocution to personnel working nearby. It is therefore necessary to detect and clear any fault quickly. The first device used in early electrical systems was the fuse, which acted both as the sensor and the interrupting device.
With larger systems, separate devices became necessary to sense and interrupt fault currents. In the beginning these functions were combined in a single assembly; a circuit breaker with in-built releases. This practice is still prevalent in low voltage systems. In both high systems and low voltage systems of higher capacities, the sensing is done by more sophisticated devices called relays. Relays were initially electro-mechanical devices but static relays and more recently digital relays have become the norm. With more complex systems, it is necessary to detect the point of fault precisely and trip only those sections affected by the fault while the rest of the system can continue to function normally.
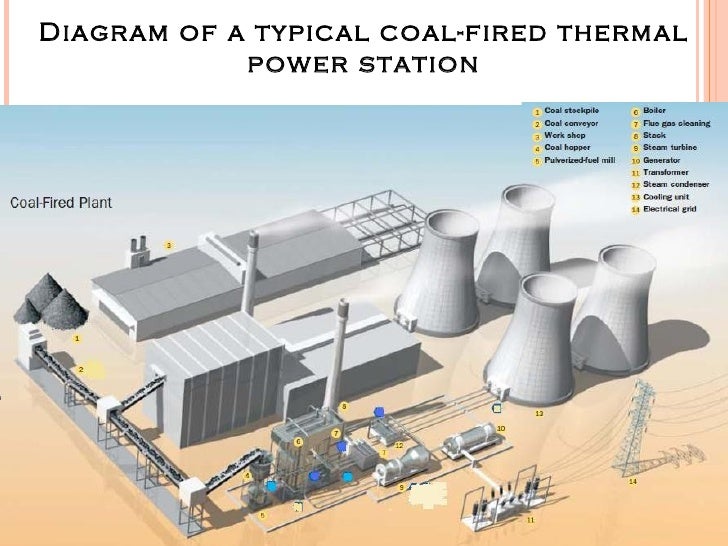
In the event of the nearest circuit breaker failing to operate, the next breaker in the upstream (feeding) side has to be tripped as a 'back up' measure. Another requirement is to minimise the time for which a fault remains in the circuit; this is necessary to reduce equipment damage and the danger to operating personnel. These requirements necessitate different forms of relaying apart from the simple current sensing relays. Equipment such as generators, transformers and motors also need special forms of protection characterised by their design and operating principles.

Aug 30, 2012. Bridging the gap between the fundamental concepts of fluid mechanics, heat transfer and thermodynamics, and the practical design of thermo-fluids components and systems, this textbook focuses on the design of internal fluid flow systems, coiled heat exchangers and performance analysis of power plant. Dec 07, 2011 Download your FREE White Paper Collaborating in SOLIDWORKS to Design a “Supertruck” When was the last time you drove down the highway without seeing a commercial.
This course will explain all of these points in detail and provide you with the skills and knowledge necessary to calculate fault currents, select relays and associated instrument transformers appropriate to each typical system or equipment. You will also learn how to adjust the setting of the relays so that the relays closest to the fault will operate and clear the fault faster than the backup devices. Benefits of eLearning to Students • Cost effective: no travel or accommodation necessary • Interactive: live, interactive sessions let you communicate with your instructor and fellow students • Flexible: short interactive sessions over the Internet which you can attend from your home or office. Learn while you earn!
Thermal Power Plant: Design and Operation deals with various aspects of a thermal power plant, providing a new dimension to the subject, with focus on operating practices and troubleshooting, as well as technology and design. Its author has a 40-long association with thermal power plants in design as well as field engineering, sharing his experience with professional engineers under various training capacities, such as training programs for graduate engineers and operating personnel. Thermal Power Plant presents practical content on coal-, gas-, oil-, peat- and biomass-fueled thermal power plants, with chapters in steam power plant systems, start up and shut down, and interlock and protection. Its practical approach is ideal for engineering professionals.
Key Features. • Dedication • Acknowledgements • Preface • List of Acronyms/Abbreviations • Chapter 1.
Steam Power Plant Cycles • 1.1 Introduction • 1.2 Laws of Thermodynamics • 1.3 Carnot Cycle • 1.4 Stirling Cycle • 1.5 Ericsson Cycle • 1.6 Rankine Cycle • 1.7 Kalina Cycle • 1.8 Binary Vapor Cycle • 1.9 Problems • Bibliography • Chapter 2. Steam Generators • 2.1 Introduction • 2.2 Boiling and Circulation • 2.3 Design • 2.4 Classification and Utilization • 2.5 Boiler Mounting and Accessories • 2.6 Superheaters and Reheaters • 2.7 Economizers • 2.8 Air Heaters • 2.9 Insulation • 2.10 Supercritical Boilers • 2.11 Problems • Bibliography • Chapter 3. Fuels and Combustion • 3.1 Introduction • 3.2 Sources of Chemical Energy • 3.3 Availability of Fuels • 3.4 Characteristics of Coal • 3.5 Other Solid Fuels • 3.6 Petroleum and Natural Gas • 3.7 Principles of Combustion • 3.8 Combustion Calculations • 3.9 Design Aspect of Burner • 3. Fsx P3d Alabeo C172rg Cut Class Iii. 10 Flame Stability • 3.11 Design Aspects of Furnace • 3.12 Problems • Bibliography • Chapter 4. Pulverized Coal-Fired Boilers • 4.1 Brief History • 4.2 Combustion of Pulverized Coal • 4.3 Pulverizer Performance • 4.4 Coal Burners (Figure 4.8) • 4.5 Pulverizer System Design • 4.6 Classification of Pulverizers • 4.7 Coal Preparation Systems • 4.8 Coal Feeders • Bibliography • Chapter 5.
Fluidized-Bed Combustion Boilers • 5.1 Brief History • 5.2 The Technology • 5.3 Categories of FBC • 5.4 Design Variables • 5.5 Bubbling Fluidized-bed Combustion (BFBC) Boilers • 5.6 Circulating Fluidized-bed Combustion (CFBC) Boilers • 5.7 Pressurized Fluidized-bed Combustion (PFBC) Boilers • 5.8 Start-Up and Loading of PFBC Boilers • 5.9 Problems • Bibliography • Chapter 6. Steam Turbines • 6.1 Introduction • 6.2 Type of Steam Turbine • 6.3 Classification of Steam Turbines • 6.4 Components of Steam Turbines • 6.5 Methods of Turbine Governing • 6.6 Turbine Governing System • 6.7 Turbine Lubrication System • 6.8 Speed Control System • 6.9 Turbine Losses • 6.10 Operating Regime • Bibliography • Chapter 7. Gas Turbine and Heat Recovery Steam Generator • 7.1 Introduction • 7.2 Ideal Brayton Cycle • 7.3 Real Brayton Cycle • 7.4 Improvement of Performance • 7.5 Gas Turbine Systems and Equipment • 7.6 Heat Recovery Steam Generator (HRSG) • 7.7 Problems • Bibliography • Chapter 8. Diesel Power Plant • 8.1 Introduction • 8.2 Thermodynamic Cycle • 8.3 Design • 8.4 Equipment and Accessories • 8.5 Diesel Engine Systems • 8.6 Problems • Bibliography • Chapter 9. Steam Power Plant Systems • 9.1 Introduction • 9.2 Mechanical Systems • 9.3 Electrical Systems • Chapter 10.
Automatic Control • 10.1 Introduction • 10.2 Automatic Boiler Control • 10.3 Automatic Control of Turbine • 10.4 Coordinated Control System • 10.5 Automatic Control of Regenerative System • Bibliography • Chapter 11. Interlock and Protection • 11.1 Introduction • 11.2 Steam Generator • 11.3 Fuel-Firing Equipment • 11.4 Steam Turbine • 11.5 Gas Turbine • 11.6 Diesel Engine • 11.7 Generator (Alternator) • Bibliography • Chapter 12. Start-Up and Shut-Down • 12.1 Introduction • 12.2 Start-Up of Steam Generator • 12.3 Normal Shut-Down of Steam Generator • 12.4 Emergency Shut-Down of Steam Generator • 12.5 Start-Up of Steam Turbine • 12.6 Normal Shut-Down of Steam Turbine • 12.7 Emergency Shut-Down of Steam Turbine • 12.8 APS • 12.9 Start-Up of Gas Turbine • 12.10 Normal Shut-Down of Gas Turbine • 12.11 Emergency Shut-Down of Gas Turbine • 12.12 Start-Up of Diesel Engine • 12.13 Normal Shut-Down of Diesel Engine • 12.14 Emergency Shut-Down of Diesel Engine • Bibliography • Chapter 13.
Abnormal Operating Conditions • 13.1 Introduction • 13.2 Abnormal Operating Conditions of Steam Generators • 13.3 Abnormal Operating Conditions of Steam Turbines • 13.4 Abnormal Operating Conditions of Gas Turbines • 13.5 Abnormal Operating Conditions of Diesel Engines • 13.6 General Electrical Faults • Bibliography • Chapter 14. Air Pollution Control • 14.1 Introduction • 14.2 Control of Suspended Particulate Emission • 14.3 Reduction of Greenhouse Gas Emission • 14.4 Methods of SOX Emission Control • 14.5 Methods of NOx Emission Control • 14.6 Reduction of Mercury Emission • 14.7 Problems • Bibliography • Chapter 15. Codes and Standards for Power Plant Design and Operation • 15.1 Introduction • 15.2 Benefits • 15.3 Issuing Organizations • 15.4 Commonly Used Codes and Standards • Bibliography • Appendix A. Power from Renewable Energy • A.1 Introduction • A.2 Solar Energy • A.3 Wind Energy • A.4 Geothermal Energy • A.5 Ocean Thermal Energy • A.6 Tidal Energy • A.7 Wave Energy • A.8 Hydraulic Turbine • A.9 Energy From Biomass • Bibliography • Appendix B. Power from Nuclear Energy • B.1 Introduction • B.2 Pressurized-Water Reactor (PWR) • B.3 Boiling-Water Reactor (BWR) • B.4 Gas-Cooled Reactor (GCR) • B.5 Heavy-Water Reactor (HWR) • B.6 Fast-Breeder Reactor (FBR) • Bibliography • Appendix C • Index.
Dipak Sarkar has over 40 years of experience in the field of Mechanical Engineering & Power Plant Operation with rich experience in Diesel Generator Plant, Combined Cycle Power Plant and Coal-fired Sub-critical and Supercritical Thermal Power Plants. During this time, he has shared his experience with professional engineers under various training schemes, like training programs for graduate engineers and operating personnel. He was recently the Executive Director of Administrative & Technology Control of Various Power Projects, and is now a Guest Faculty in the Department of Power Engineering at Jadavpur University.